Plastic extrusion transforms raw polymers into continuous shapes with consistent dimensions and properties. This versatile manufacturing process serves industries such as construction, automotive, packaging and consumer goods. At Naphtha Plastics we provide high-performance materials optimised for two primary extrusion methods.
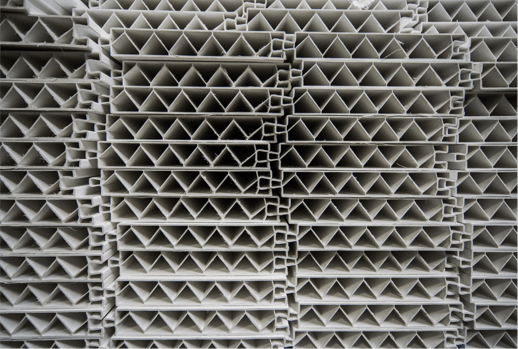
SHEET EXTRUSION
Plastic sheet extrusion is a continuous process used to manufacture flat sheets of plastic in a wide range of thicknesses and widths. These sheets are then used in thermoforming, fabrication, packaging, signage, construction, and automotive applications. As this process depends on precise control of melt flow, temperature, and cooling, the quality and consistency of raw polymer is critical.
At Naphtha Plastics, we supply high-performance thermoplastics to sheet extruders looking for dependable, cost-effective material supply. Our broad portfolio includes prime and recycled materials, allowing customers to achieve the right balance of mechanical performance, aesthetics, and sustainability.
.webp?width=2656&height=1794&name=Naphtha%20Plastics%20(16).webp)
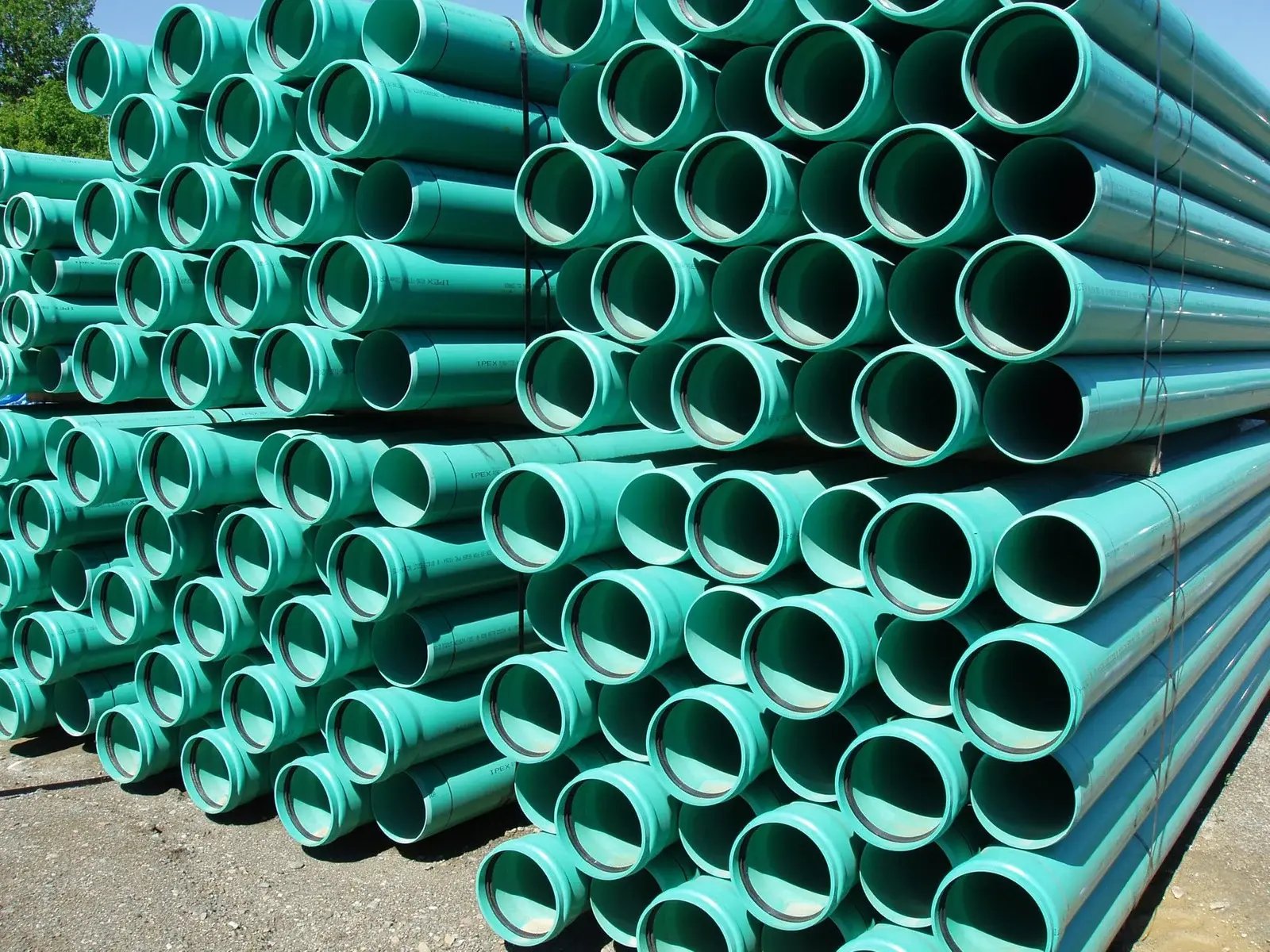
PROFILE EXTRUSION
Profile extrusion creates continuous, shaped products like pipes, tubes, weather seals, cable ducts, window profiles, and custom components. These profiles often serve structural or functional roles, making material selection critical for strength, flexibility, UV resistance, and impact performance.
Profile manufacturers face challenges of precision, complexity, and durability. The process frequently involves multi-cavity dies, complex cross-sections, and tight dimensional tolerances. Poor-quality raw material leads to die build-up, inconsistent output, brittleness, or end-use failure. Many profiles must also meet outdoor durability or electrical insulation standards.
We support profile extruders with high-purity materials that flow evenly and cool predictably, offering both flexible and rigid polymer grades, customised compounds with specialised additives, and recycled polymers to reduce environmental impact.
Challenges & solutions
THE CHALLENGE: UNIFORMITY, STRENGTH, AND AESTHETIC QUALITY
With extrusion, even minor fluctuations in polymer quality can cause problems such as thickness variation, surface defects, warping, or poor thermoformability. These issues result in increased scrap rates and rejected product, especially in applications that require tight tolerances or high visual standards.
OUR SOLUTION: RELIABLE POLYMER SUPPLY FOR CONSISTENT OUTPUT
Working with Naphtha Plastics provides extruders with:
- Consistent, well-characterised polymers that ensure smooth extrusion and uniform gauge.
- Custom material blends to meet optical, impact, or thermal performance needs.
- Recycled content options that meet regulatory and customer sustainability goals.
- Technical guidance on material compatibility, processing temperatures, and downstream applications.
AVAILABLE MATERIALS
Stable and repeatable extrusion performance, reducing downtime and scrap.
Faster setup times and fewer material changes thanks to reliable supply.
Support for cost control through recycled content and value-engineered materials.
Responsive customer service, with fast turnaround on orders and technical queries.
Working with Naphtha Plastics will ensure your extrusion lines stay efficient and productive.
LET'S TALK!
We're always happy to have a chat about plastics. Fill in the form and we'll get back to you. Or, let us know you're calling in at Naphtha Plastics for a cuppa, and we'll get some biscuits in!
Woodhill Works
Woodhill Street
Bury
Lancashire
BL8 1AT